Prelude To Our Summer 2019 Cruise. Our first big problem for the Summer 2019 cruise was the discovery in early April that Kap’s Nexus card had expired just four days earlier. That was a real heart-sinker, as we knew months earlier that it had to be renewed. I had set up a calendar reminder but it had somehow disappeared.
Don’t forget – you can click on any photo in the post to enlarge it.
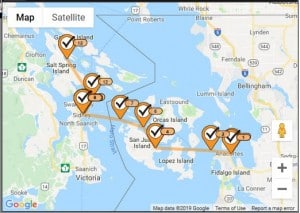
Here's what the SPOT map looks like if you click on Current Location in the upper right corner of the blog Home Page, showing each of the position tags from our Anacortes departure, across to Friday Harbor, across the U.S./Canada border to Sidney, and then north to Ganges.
If you want to see where we are now, or better yet, monitor our route progress as we cruise along, you can go to www.ronf-flyingcolours.com and click on the Current Location link in the upper right corner of the home page.
Also, if you’re reading this post in the e-mail version, it’s much more readable in the online version, plus you can read any of the posts back to 2010 from the archive – just click on the link above to access the blog.
For ten years now we’ve relied on our Nexus cards for crossing to/from the Canadian/U.S. border. Nexus is also known as the Trusted Traveler Card to both U.S. and Canadian Customs and Border Patrol (CBP) – allowing us to cross the border in each direction by simply telephoning a special 800-number when our GPS on the boat tells us we’re crossing the border. This is hugely beneficial to us, as it allows us to bypass the Customs dock at the nearest port of entry on our crossings, and because we’ve already had extensive background checks with CBP years earlier, the fuss with the border agents is always very minimal and much more worry free.
(Having a Nexus card also makes life significantly easier in other ways. You automatically have TSA Pre-Check status for the otherwise huge hassle at airport security – which can easily save an hour of frustrating wait time in the long airport security lines these days. It also means a special Nexus car lane on both sides of the border crossings between the U.S. and Canada, and with the frequent, and incredibly long wait times at our crossings near Bellingham, having Nexus can easily cut an hour or more at each crossing – crossings we’ve made several times this past year. And entering the U.S. from any international flight, having a Nexus card gives you access to the Global Entry kiosks at Passport Control, allowing you to scan your card at a self-service kiosk and you whisk through the otherwise long lines in minutes (if not seconds). The whole process of getting a Nexus card can take up to six months, but if you’re doing any of these travel options, it’s well worth it. If this information piques your interest, you can begin the application process by going to https://ttp.cbp.dhs.gov/, and click on the Get Started link under the Nexus heading. It costs $50 per person, which is a real bargain, given how beneficial it is.)
As soon as our renewal mistake was realized, I logged onto our online CBP account and filled out the renewal form to see if a late renewal was possible. It very clearly wasn’t, and making it worse, the Nexus renewal page indicates that the government shutdown last January has created significant delays in new Nexus applications as well as renewals – and now a renewal can take months for completion. (My guess is, the government shutdown created an initial lengthening of processing time, but shifting people off to other duties to cover for the contrived, stupid, and unnecessary border crisis is the real cause.)
Anyway, since early April I’ve checked the CBP web site daily to see if Kap’s renewal has come through, and it hasn’t. That means an at-the-dock Customs clearance into Canada on this trip would be necessary, something we haven’t done for the last 10 years of cruising on Flying Colours, and that raised my anxiety level.
Preparations For Departure. Since it’s really crucial to have all of our ducks in a row by dock departure time for the summer’s cruise, I’ve created – and added to – an extensive Excel spreadsheet checklist that’s now at 160+ To Do items. Starting in the Fall, the checklist identifies all of our annual maintenance items for the boat – such as engine and transmission maintenance and oil changes, repair and maintenance on all other mechanical or electrical systems, and upgrades and maintenance for our electronics – navigation and otherwise. It also includes general boat repairs and maintenance, such as teak rail varnishing, carpet cleaning, minor fiberglass ding repairs and anything that’s had a problem during our most recent cruise. Every other year we require a haul-out to check things below the waterline, including hull cleanup and bottom paint, and replacement of zincs that protect us from “hot” marinas.
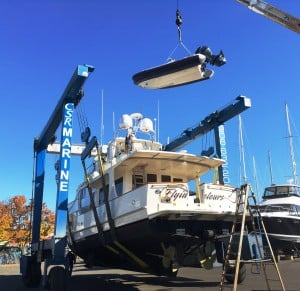
As part of the haul-out for bottom paint, we had the dinghy removed by crane, then drove is out the Ballard Locks and north to Edmonds to have a new (smaller) outboard motor fitted.
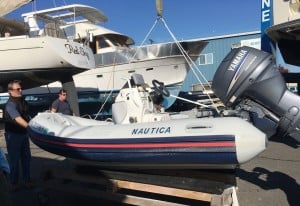
Doesn't that 40 HP Yamaha outboard motor look too big for the dinghy? It was great for getting us up to 22 MPH on the way out and back to set and pull prawn pots, but it had its problems. The new 25 HP motor will hopefully be much better, albeit slower.
This year, given that Flying Colours is 10 years old, we had some special things done. We’ve regretted it for years, but when we visited the huge Fort Lauderdale Boat Show just before taking delivery of Flying Colours in 2009, the East Coast Fleming dealer at the show talked us into getting our inflatable dinghy from a Florida manufacturer – who turned out to be a real shyster, and we were glad to hear, is now out of business. The dinghy itself is OK, but he convinced us to get an outboard motor for it that’s too large (heavy) and powerful (40 HP) for a dinghy of its size. As a result, it’s never been easy to get the dinghy up on a plane – which is necessary when you transition from about 10 MPH to anything higher – because the weight of the outboard keeps the nose of the dinghy too high in the air. Kap has always had to lean way out on the nose to get enough weight there to bring the nose down. Worse, the motor weight somehow makes the dinghy skittish at higher speeds (18+ MPH) and we/ve just never felt safe. Last fall, we found that a local Yamaha dealer would take our outboard in on trade, and downsizing to a brand new 25 HP motor would cost us only $3,000 – which was far lower than I expected it to be. So, while Flying Colours was “out on the hard” for maintenance, we had the dinghy taken off by crane, put in the water just inside the Ballard Locks. It was then driven north to Edmonds to have the replacement motor installed. What a hoot taking a dinghy through the locks!
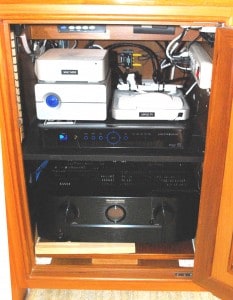
Here's our new entertainment system rack of gizmo boxes. They're now state-of-the-art digital devices - which really means that it'll take us months and months to figure out how to work things. Behind the boxes is a tangle of cables that would confound a Double-E PhD.
Another big ticket item (actually, one of several) was our entertainment system – the stack of electronic equipment, hooked together with a maze of wires inside a single cabinet in the boat’s salon (living room) that provides our TV and music throughout the boat. At 10 years old, it too is long in the tooth, with several analog “boxes” that are now digital in today’s world, and are so far out of date that parts and repair aren’t very easy at this stage (imagine getting service on your old Apple iTouch music player which is from the same era). We bit the bullet (to spend about 10 grand) on several new components, most of which make no sense to me whatsoever, as we decided long ago that oversight of the myriad of clickers needed to talk with all of this is something I want no part of.
While we had the A/V guy on the boat to do his thing, we also had him upgrade the WiFi system so that we can better access the internet, not only by connecting up with each marina’s WiFi system, but also using the cell towers within a 40-mile range while on the move.
Lastly, we had the boat hauled out and every-other-year bottom paint was applied – a special “anti-fouling” paint that keeps barnacles and other crud from sticking to and growing on the bottom.
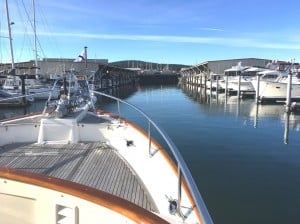
On a crisp early December (2018) morning, Kap is turning us down the fairway to our slip at Anacortes Marina.
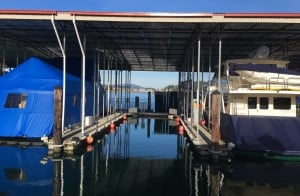
The last 60' is the trickiest - but over the years Kap has become a pro - spinning us 90 degrees into the narrow slip that Flying Colours lives in. Theslip roof is only 20' off the water line, so it's critical that we lower the 16' tall radio antennas and the radar arch that's on a clever motorized hinge that's operated with a handheld remote.
All in all, it took us over three months for this work to finish up, and it wasn’t until December 3rd that we took Flying Colours back home to Anacortes. By then, the days are really short – too short for a comfortable one-day cruise, so we turned it into a leisurely 3-day cold-weather cruise, first to Bainbridge (the town that used to be Winslow, on Bainbridge Island), then northward to Port Townsend, and finally across Admiralty Inlet (that connects to Puget Sound) to Anacortes. Basically, it was a shakedown cruise after all the maintenance, to ensure that everything was now working OK.
Then the checklist moves into the Spring, where every detail necessary to get ready for our upcoming cruise is identified and kept track of. Each year we offload a bunch of things from the boat and store them in our rented storage shed at the Anacortes Marina – things like bicycles, kayaks, prawning gear, and lots of renewable supplies. All of those have to go back aboard.
On a related worksheet – that I’ve named Pantry – I have an extensive list of every consumable pantry item on the boat, updated and accurate as of each summer’s departure. There are 6-8 cupboards around the galley area where pantry items get stored – crammed in tight is a better term. The last thing I want to do every time a box of spaghetti, or a can of chicken broth, or a package of taco spices has to be located, is to rummage through these cupboards looking for it. The Pantry spreadsheet lists every item and identifies where it’s located. Because we’re out for at least two months each summer, I stock the pantry for everything we’ll need throughout that time, and as we use up these consumables I update the spreadsheet. It’s all a pain in the butt, but it’s well worth it when it keeps the pandemonium down when I’m in the middle of cooking or getting ready for shopping.
In the weeks and months before departure each year, I also use the Pantry worksheet as a shopping list. It typically takes over a half dozen trips in the spring to get the boat provisioned and loaded, and on each trip the car is usually loaded to the gills.
Away, For Summer 2019 Cruise
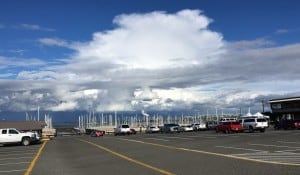
On our arrival at Anacortes Marins on departure day, an ominous thunderstorm build-up didn't promise good weather. Next morning, though, all signs of it were gone.
Monday, June 10; Anacortes Marina to Friday Harbor SYC Outstation. Finally, after what seemed like an interminable process of getting Flying Colours ready – including several delays due to various situations – we declared it time to go. Our long-settled plan has been to head north fairly quickly, bypassing or spending minimal time at our usual haunts in Desolation Sound and The Broughtons, in order to be in Wrangell, SE Alaska, for Kap to run in their Bearfest 2019 Half Marathon on Sunday, July 29th. Until our departure, though, so many things were going wrong that we weren’t sure if we’d get anywhere close to SE Alaska on this summer’s cruise, so our entire float plan has been up in the air.
The last big problem before departure was our BBQ – which seems like this should really be a minor problem, but it wasn’t. We BBQ a lot on the boat, and our freezer is packed with “stuff” that is planned for BBQ’ing throughout our cruise. As a prelude to this problem, last fall we’d realized that our two RV-type 2½ gallon propane tanks on the boat were due for re-certification (U.S. law is that new tanks have to be re-recertified 12 years after manufacture, and our tanks on Flying Colours were at that age). During our fall maintenance we took them to a marine supply store in Seattle. They were returned to us recertified, full of propane, and ready to go for another 5 years. (Complicating it, Canadian law is different on this, and with our tanks already out of certification in Canada, we can’t refill in Canada with propane until we get that sorted out – and in the meantime we need to enter Canada with enough propane to last the summer.)
We moved aboard Flying Colours on Friday night, hopefully needing just Saturday to get our last minute details sorted out, then depart Sunday morning for Sidney (B.C., on Vancouver Island). On Saturday night, we decided to BBQ and eat on the boat, but when Kap fired up the BBQ it was obvious something was wrong. Switching tanks didn’t help, even swapping out our brand new BBQ with our backup BBQ didn’t fix the problem. There was no evidence of a leak anywhere along the gas line between the tanks and the BBQ. That left the regulator as the likely culprit, even though we’d had that tested last fall too. Dinner was instead prepared on the cooktop.
Saturday morning I drove over to Mt Vernon to a propane service company that we’d worked with several years ago. From the description, the service guy felt that the likely problem was the propane tanks – maybe overfilled – but just in case, he replaced our regulator for a mere $13 (which is cheaper than anything else you ever replace on a boat). Back at Flying Colours, sure enough the new regulator didn’t solve the problem, and by now the weather had deteriorated and Kap wanted to delay until Monday morning.
Besides, it was unthinkable to leave without this problem resolved. At midday I headed off with the two propane tanks to the local Ace Hardware (where we normally have them filled). I managed to get Jerry, the most experienced propane person at Ace, to look at the tanks, and she concluded that one of them was definitely over-filled with propane. She felt the other tank was half full of propane at the time the recertification was being done and they somehow filled it the rest of the way up with plain old compressed air – and then somehow filled the other tank twice by mistake. (This was all speculation, so who knows?) By safety regulations she couldn’t help with either problem (too volatile and dangerous) – but she demonstrated exactly how I could purge the compressed air out, and suggested that we hook the overfilled tank up to our BBQ and just let it run until the overfilled propane was resolved. Back at the marina parking lot, I took the compressed air-filled tank to a remote part of the lot, cracked open the valve, and spent the next half hour listening to the hissing air bleeding off. When I thought it was almost all gone, I headed back to Ace to have it filled properly.
On return to Flying Colours with what I thought was a success, Kap hooked the tank up to the BBQ, and sure enough, it appeared the problem was resolved – enough so that we felt comfortable heading out.
Early Monday morning we made our last minute preparations, and by 9AM we were ready to go. As Kap did the normal engine warm-up, I unhooked us from the shore power at our dock and got our moorage lines untied. Kap put both engines in gear, and rather than the smooth and easy pull away from the slip the whole boat gave a shudder and a heavy vibration – obviously, something was going wrong between the engines and props.
Geez, Louise! What else can go wrong? Kap immediately shut down and we re-tied Flying Colours to the dock cleats. She then restarted the engines, put one engine at a time in gear for just a second as we tried to determine which one (or both) was causing the problem. It was obviously the port-side engine/prop. We’d had a similar experience several years ago after the boat was sitting in our slip unmoved for several months, we figured it might be something similar – kelp, barnacles, whatever – that had grown on the props or prop shafts in the past few months, causing things to be out of balance. But that didn’t make sense, as we’d just had our local marina diver dive on the boat the previous week to check our zincs for wear and tear, and he said the bottom looked in beautiful shape. We then called Chris, our go-to service in Seattle, and he had some ideas, but didn’t point to a solution. Kap was resistant to my idea, but with Chris’ concurrence I managed to talk her into more securely tying to the dock, and again, one engine at a time, putting it in gear for a longer time to see if the problem would work itself out. Sure enough, after doing this about a half dozen times the port engine/prop smoothed out – and we now felt much more comfortable to head off. What the problem was, though, we’ll never know.
We still had to top off our main diesel tanks at the next door marina fuel dock and by the time we got away, it was almost 2PM. With a 2+ hour cruise over to the Seattle Yacht Club Outstation at Friday Harbor, I was concerned that we’d be the last arrivals of the day, and it made it iffy as to whether we’d get a moorage spot. This stopover at Friday Harbor was intended to be our shakedown cruise, where we’d spend a couple of days testing out as many systems as possible to ensure that everything was working OK.
So finally being away from Anacortes, at least we got some water under our bums, and even if it came with a lot of frustration, the worst day on a boat is better than the best day on land.
Next up: Two days at Friday Harbor, then over to Sidney. Stay tuned.